Projects
Hello again; I welcome you to my portfolio. These are the projects I have done and been a part of from the year 2020 to 2022. If you would like a more compact portfolio, please click here.
Joro, The autonomous land surveyor
Aim: Design an autonomous land surveying robot.
​
About the design
Navigation and Mapping: A machine understanding the world in 3D requires a spatial understanding of the environment and its position and orientation in space. This is achieved with the Intel RealSense Tracking Camera T265, rigidly coupled and spatially aligned with the Intel RealSense Depth Camera D435. The Intel RealSense
Tracking Camera T265 estimates its position and orientation relative to a gravity-aligned static reference frame. At the same time, the Intel RealSense Depth Camera D435 performs stereo matching to obtain a dense cloud of 3D scene points. Together this input can be used to get the point cloud registered with respect to a gravity-aligned static reference frame. The two cameras are mounted onto a camera holder that is mounted on top of Joro’s top cover. The camera holder is 3D printed.
Next to the cameras is a 3D LiDAR sensor. The sensor had to be mounted at a slightly higher level than the cameras because the cameras would constantly get in the way of the sensor. Last on the Navigation and mapping components are the GNSS and the GPS. The GNSS and the GPS will enable the robot to know its exact location anywhere on Earth, with the apparent exceptions like inside large bodies of water or deep underground. This enables Joro to survey and navigate an area with no previous data recorded. The D435, T256, 3D LiDAR sensor, GPS, and GNSS are connected to the Nvidia Jetson nano or Raspberry pi4. It is the central processing unit for Joro.
​
Motion: The ESC (Electronic Speed Control) is connected to the Nvidia Jetson nano. It receives commands from the central control system and moves the motors as instructed. The motors are connected to the 8-inch pneumatic wheels, which gives the robot a ground clearance of 66 mm. Joro is driven by four motors, one motor per wheel. The Nvidia Jason nano is fitted on top of the middle plate, along with most other essential chips and batteries.
​
Land Marking: The robot uses a 500 ml temporary water miscible marking paint designed for spray application in a vertical or upside-down position. It provides exceptional quality in color brightness, retention, durability, and color consistency. The sprayer is connected to the ROS, which gets the instruction to trigger the spray.
​

Multi-level Mobile Greenhouse
Aim: Introduce agricultural means to South African townships and urban areas.
​
About the design
The greenhouse has 20,000 liters of space. The greenhouse's suspension system (made of 2 axles with drum brakes and 4 four leafed springs) and the greenhouse's supports increase the steadiness of the whole structure. The drum brakes are mechanical and electrical, allowing the locking of the four 15-inch rims and 18-inch wheels while the greenhouse operates in a stationary position. The four supports are strategically positioned in the front and rear ends of the trailer base to create a steady structure.
The trailer base has evenly spaced metal bars for the sole purpose of holding up the flooring of the greenhouse and the greenhouse itself. The wooden floor sits below the rubber floor; this flooring stores more heat for the greenhouse and is easier to clean. The first seven frames, including the first, are placed evenly apart from the last two frames.
​
The polycarbonate boards/panels of the greenhouse are installed on the exterior of the greenhouse. Although the left side is slanted, the 3 level shelves are still vertically straight. This creates a passage in the middle of the greenhouse with the extended shelves without being a hindrance. This was achieved by varying the lengths of the shelves from the bottom to the top shelves. No shelves are installed on the front-end frame; this was purposely done to allow more room in the greenhouse and for growing plants requiring more height. The shelves can be collapsed to give the user more freedom to do what they want by effectively utilizing the space created when the shelves are collapsed.
The ramp has two resting positions; the first position is when the greenhouse is at rest, the supports are extended, and the ramp is lowered in position. The second position is when the greenhouse is in motion, and the ramp is retracted and attached to the rear frame. The actuators of the greenhouse are a digital thermometer and a hygrometer. The greenhouse uses fluorescent lights and an air conditioning unit for light, heating, and cooling. The panels can also be opened to create a partly closed greenhouse.
​

Automated Guided Vehicle (AGV)
Aim: Design a lightweight material handling AGV.
​
About the design
The lightweight material handling AGV is powered by a 12 Volts and 7 A lead battering. The control board is the system for receiving and sending signals to other components on how they should function. It controls all the components in the AGV, such as the speed of the motors that drive the wheels, the speed of the robot arm to pick up and lift down the materials, the magnetic navigation sensor to track the magnetic tape, etc.
A magnetic sensor can detect and report the position of a magnetic field along its horizontal axis. This sensor is installed in the AGV and reads the magnetic tape on the industrial floor. The sensor is built with advanced signal processing to accurately measure its lateral distance from the center of the track with millimeter resolution resulting in nearly 160 points end to end; it detects and manages up to 2-way forks and can be instructed to follow the right or left track. It tracks heights up to 60 mm and with a 10-millisecond update. The magnetic tape can be hidden under non-ferrous flooring materials such as parquet, tiles, or carpet.
​
AGV forklift wheels are the center drive wheels, and their function is to control the motion and steering of the AGV. Two steering /braking motors are connected to the sides wheel and the motor in the middle, which deliver a 4kW at 48V nominal voltage. The remaining four wheels will be moving freely. The stepper robotic arm picks up and drops light weighted materials. AGV body protects the interior components of the AGV. The four ultrawide cameras assist in controlling the movement of the AGV. The AGV scans objects around it using these cameras to prevent accidents in the workshop.
​

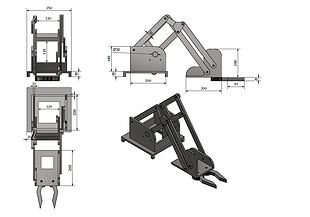

Legume dehuller
Aim: Design an effective legume dehulling machine with reduced noise pollution.
​
About the design
The machine is divided into two main components, the conveyor and dehulling chamber. The grain is inserted in the hooper on top of the conveyor. The grain is gradually transported to the dehulling chamber by the helical screw. The helical screw moves relative to the abrasive disc shaft. The conveyor cover covers the helical screw.
The conveyor has an air vent; this allows the dust from the grains to leave the dehulling machine and reduces the impact of the dust on the bearings. The conveyor has a magnetic rod attached to the magnetic socket to protect the dehulling machine from unwanted metals that may enter along with the grain. It is removable, so all the metals can be removed from the magnetic rod after at least five operations.
​
After the grain leaves the conveyor, depending on the type of legume, some hulls would have already separated from the kernel. The grain enters the dehulling chamber, where the rest of the hulls are removed. The abrasive discs, with their rough surface, complete the dehulling process. The abrasive discs are attached to the abrasive disc shaft that rotates with the use of the abrasive shaft motor. 2 abrasive discs in the dehulling chamber are placed at an angle, one at the entrance and the other at the exit, the is mostly for grain-directional purposes and increasing the overall efficiency of the dehulling machine.
The Dehulling chamber is where all the dehulling chamber components are attached. The dehulling chamber also has an extended support structure that is mounted to it; this is to support the conveyor above. The support structure is also a platform where the conveyer motor plate is attached.
​


Structural and Thermal Analysis of brake discs/ rotor
Aim: The project aimed to investigate: the effectiveness of gray cast iron and stainless steel on different types of rotors and determine the effectiveness of each rotor. Both ANSYS and Autodesk Inventor were used to conduct the simulation.
​
Results
The models were derived from the classic mini cooper; the dimensions were kept the same to retain consistency in the results. When a force of 1500N is applied on both sides of each rotor, the solid rotor deforms more compared to the ventilated and ventilated, and drilled rotor, and the ventilated rotor deforms more than the ventilated and drilled rotor. The solid rotor experiences more stress compared to the other two rotors. The performance of the two materials (gray cast iron and stainless steel) is more or less the same, and the differences in the stresses are negligible.
The rotors made of gray cast iron deformed more compared to the same rotor made of stainless steel. The solid rotor is used on smaller cars (Hyundai i10, i20, Toyota Etios, Chevy spark, etc.), the ventilated rotor is used on some sedans and most SUVs, and the ventilated discs are found on more luxurious sedans and SUVs. The ventilated discs are excellent at dissipating heat, which is a wanted attribute of the performance of rotors. Further research shows that the bigger the radius of the rotor, the better the rotor is at dissipating heat. Ventilated and drilled rotors are strategically drilled not to compromise the rotor’s structural integrity, which would shorten the life span of the rotor and cause unwanted failures.
​